At any given time, we have a wide selection of amazing 'ready to wear' leather jackets which can be purchased and dispatched to you the next working day. However, if you want the full Aero experience, there really is no substitute for getting your own Aero jacket made to order. That way, we can truly make your dream jacket — one that fits you correctly and is made from the exact materials you want, right down to the hardware.
Below, we’ve outlined the process of creating your own Aero, from starting as perhaps a vaguely formed idea in your mind to finally seeing yourself wearing your dream jacket in front of a mirror for the first time.
Below, we’ve outlined the process of creating your own Aero, from starting as perhaps a vaguely formed idea in your mind to finally seeing yourself wearing your dream jacket in front of a mirror for the first time.
Before ordering:
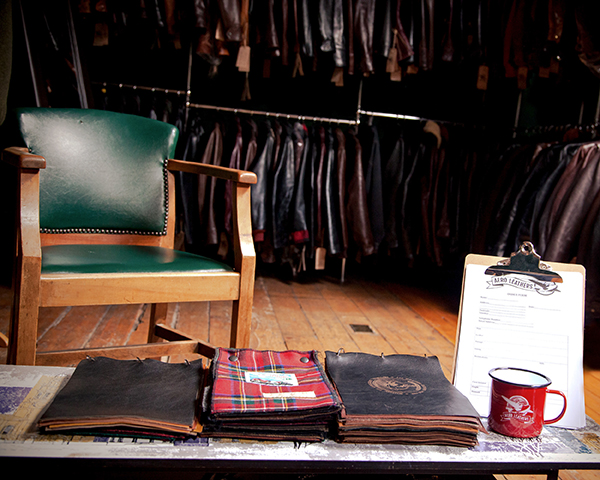
We understand that buying your own Aero jacket (especially your first) is a considered purchase, especially with so many choices to make. Which style should you choose? Which leather will work best? How do you get the right fit?
If you’re able to make the journey, we’d be delighted to book you in for an appointment to visit our factory/showroom. That way, we can have a chat about your options and take your measurements in person, plus you can see and try on many examples of our styles and leathers in the flesh.
If you’re able to make the journey, we’d be delighted to book you in for an appointment to visit our factory/showroom. That way, we can have a chat about your options and take your measurements in person, plus you can see and try on many examples of our styles and leathers in the flesh.
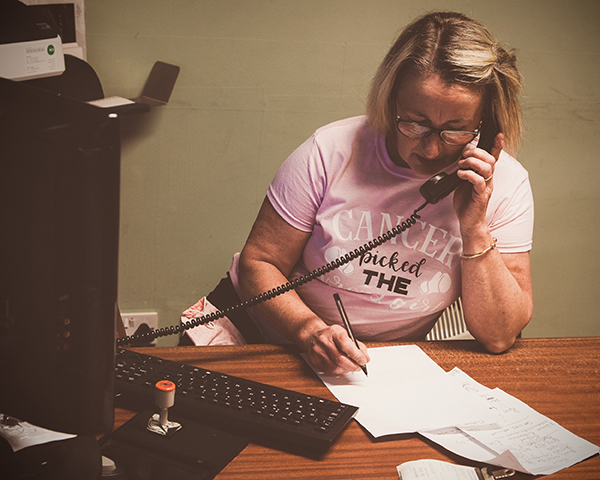
While this is the ideal way to make on your selections, we understand that this journey is not possible for many of customers who are further afield, so we’ve made sure the online Aero experience is as close to being here as possible. We have placed as much information as we can on our website (both within the product listings and within the personalisation pages that follow), to inform you about our styles and materials and let you know how to provide us with accurate measurements. There is also further information breaking down industry terms and our own processes within the FAQ section of our website.
If you can’t find the information you’re looking for on our website or you are having trouble deciding, our experienced and friendly customer service team are always on hand to help in any way we can. We can send leather samples and photos of jackets/materials and use the knowledge and experience we’ve built over decades to guide you through each decision and advise you what we think will work best until you’re happy with what you’ve ordered. Over the years we’ve helped thousands of customers create their dream jacket, so please don’t hesitate to get in touch - it’s our favourite part of the job!
If you can’t find the information you’re looking for on our website or you are having trouble deciding, our experienced and friendly customer service team are always on hand to help in any way we can. We can send leather samples and photos of jackets/materials and use the knowledge and experience we’ve built over decades to guide you through each decision and advise you what we think will work best until you’re happy with what you’ve ordered. Over the years we’ve helped thousands of customers create their dream jacket, so please don’t hesitate to get in touch - it’s our favourite part of the job!
Ordering your jacket:
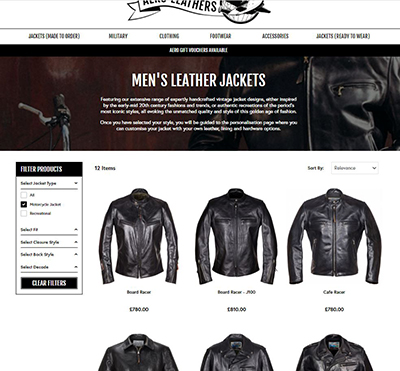
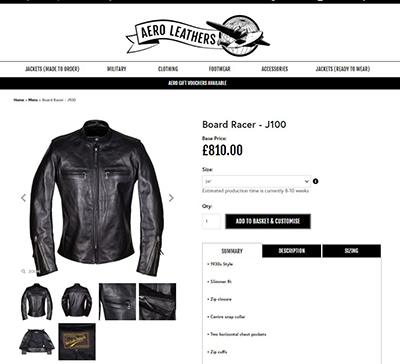
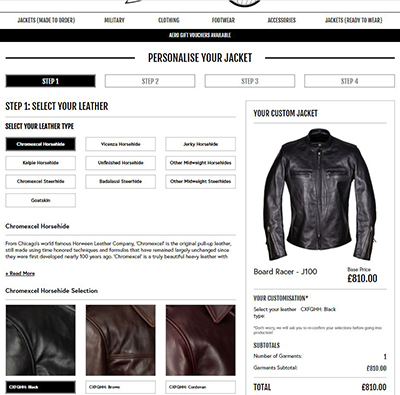
The best way to order a jacket from Aero is via our website – we’ve done lot of work to provide you with all the information you’ll need to make your decision, but if you need any help, our team is on hand via email/phone to assist you.
The first decision to make is which style you’d like from our wide range of early 20th century designs in our Made to Order and Military departments. We have over 100 to choose from, but you can easily dial in on the type of jacket you’re looking for by using the product filters on the left-hand side of the screen. You can find a summary of each jacket’s features and a wider contextual description within the jacket listings. Please note: the jackets pictured in each listing are just examples – you will be able to choose your own leather options etc later in the process.
Once you have chosen a style, you can select which size you want within the product listing. This may not always be the size you are used to ordering depending the style you’ve chosen, but there is a sizing information summary within the product listing as well as further information on sizing available in our FAQ section to help guide you. Don’t worry, our team of sizing experts are also on hand to assist and will check over the measurements you provide later in the process against your size and let you know if there any issues.
Once you have ordered your style and size, you will be taken through to the personalisation pages to select your leather, lining, hardware and extra options (such as inside pockets). We have a wide selection of options in each category and provide pictures and information on each to assist you in picking the options that are right for the jacket you’re creating. If you’re still unsure about your selections at this point – don’t worry! We’ll check over your order and then re-confirm all your selections later in the process before going into production. We won’t put your jacket into production until you’re sure about your selections.
The first decision to make is which style you’d like from our wide range of early 20th century designs in our Made to Order and Military departments. We have over 100 to choose from, but you can easily dial in on the type of jacket you’re looking for by using the product filters on the left-hand side of the screen. You can find a summary of each jacket’s features and a wider contextual description within the jacket listings. Please note: the jackets pictured in each listing are just examples – you will be able to choose your own leather options etc later in the process.
Once you have chosen a style, you can select which size you want within the product listing. This may not always be the size you are used to ordering depending the style you’ve chosen, but there is a sizing information summary within the product listing as well as further information on sizing available in our FAQ section to help guide you. Don’t worry, our team of sizing experts are also on hand to assist and will check over the measurements you provide later in the process against your size and let you know if there any issues.
Once you have ordered your style and size, you will be taken through to the personalisation pages to select your leather, lining, hardware and extra options (such as inside pockets). We have a wide selection of options in each category and provide pictures and information on each to assist you in picking the options that are right for the jacket you’re creating. If you’re still unsure about your selections at this point – don’t worry! We’ll check over your order and then re-confirm all your selections later in the process before going into production. We won’t put your jacket into production until you’re sure about your selections.
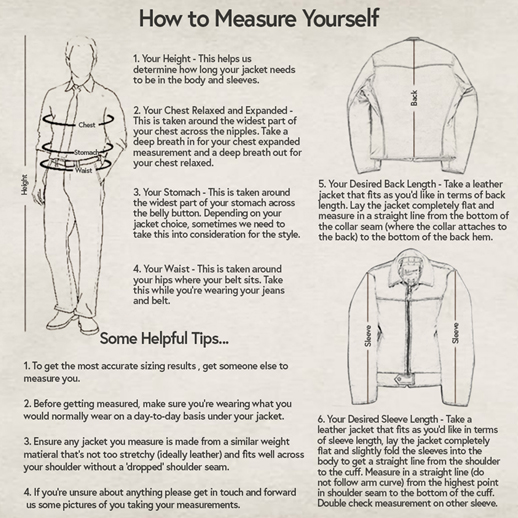
You will then be asked for a selection of measurements to help us ensure you’ve chosen the right size and to determine the correct lengths of your jacket. Again, we have information within our FAQ section and our team are on hand to help you with any measurement related queries you may have.
The final stage of placing your order is letting us know your contact/delivery/billing details if you don’t already have a registered account with us. You have the option to pay your full balance for your jacket or you can pay a 25% deposit and pay the rest upon the jacket’s completion.
Once you have completed your order, you will receive an email confirming the order has been placed and we’ll be in touch over the next few working days to approve the order.
The final stage of placing your order is letting us know your contact/delivery/billing details if you don’t already have a registered account with us. You have the option to pay your full balance for your jacket or you can pay a 25% deposit and pay the rest upon the jacket’s completion.
Once you have completed your order, you will receive an email confirming the order has been placed and we’ll be in touch over the next few working days to approve the order.
Pre-production:
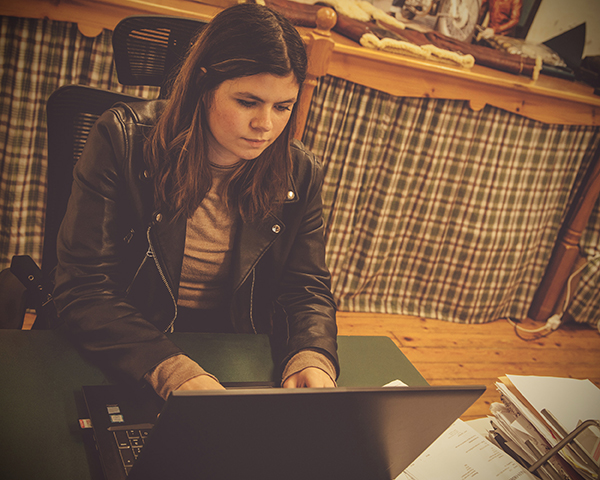
A week or two after placing your order, one of our production assistants will check over the measurements you’ve supplied against your selected size and your material selections. If there are any issues, we will contact you back to advise you and suggest an alternative sizing option/material selection. Otherwise, we will send you an email to confirm your order has been accepted, give you an estimated completion date for your jacket and that we will be in touch after 14 days for final confirmation of these specifications.
After 14 days, we will send you another email to confirm your final jacket specifications. Once you have confirmed these your jacket will enter the production queue, awaiting a production slot in our factory. Once a slot becomes available, we will send you an email to confirm when your jacket has entered production.
After 14 days, we will send you another email to confirm your final jacket specifications. Once you have confirmed these your jacket will enter the production queue, awaiting a production slot in our factory. Once a slot becomes available, we will send you an email to confirm when your jacket has entered production.
Cutting
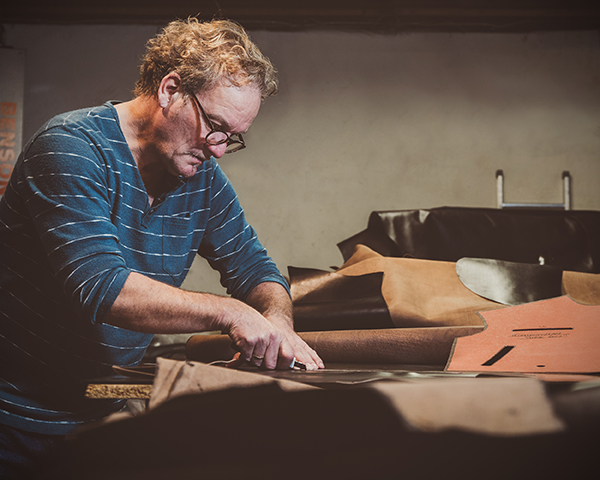
The first stage of your jacket’s production is cutting. We never cut batches of leather panels in a production line style run. Even though it's a much more economical way to work, the risk of mismatched panels is high when compared to a jacket where each panel is matched to the next during cutting.
Our specialist leather technicians have decades of experience working with a vast range of quality leathers. They select and quality-inspect each hide before skilfully hand-cutting every panel individually for your jacket – matching colour, grain, weight, and characteristics with expert precision. These panels, alongside your lining which is hand cut to your measurements by our lining/pattern technician, are then quality checked by our production manager before being passed on to your jacket’s machinist.
Our specialist leather technicians have decades of experience working with a vast range of quality leathers. They select and quality-inspect each hide before skilfully hand-cutting every panel individually for your jacket – matching colour, grain, weight, and characteristics with expert precision. These panels, alongside your lining which is hand cut to your measurements by our lining/pattern technician, are then quality checked by our production manager before being passed on to your jacket’s machinist.
Machining
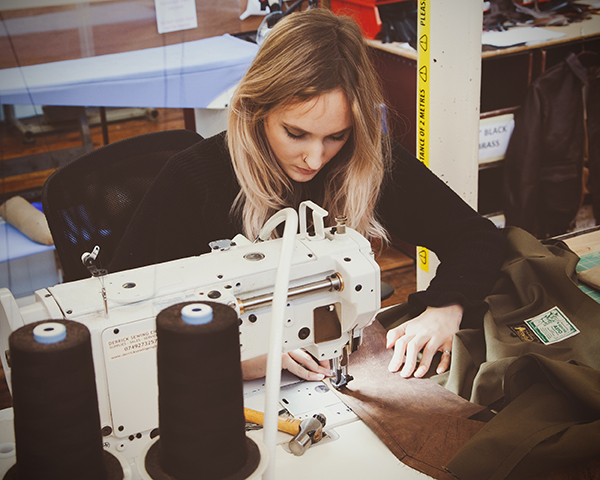
Again, we don’t adopt a time-saving production line style approach to sewing – your Aero jacket is made on a traditional walking foot machine by one experienced and highly skilled craftsperson. Making an Aero demands craftmanship of the highest calibre – many of our machinists have several decades of experience in their craft and work alongside some of the finest graduates of the world-famous Heriot Watt Textile University (the UK’s leading textile university).
Over the course of many hours, one of our skilled artisans will stitch together your jacket from start to finish with painstaking attention to detail and enormous care, using heavy duty cotton thread with a poly core for extra strength and the optimum stitch size for the type and weight of leather being used. Once your jacket is complete, the maker will proudly write their name on the inside label and swing ticket of the jacket so it can be identified as one of their works.
Over the course of many hours, one of our skilled artisans will stitch together your jacket from start to finish with painstaking attention to detail and enormous care, using heavy duty cotton thread with a poly core for extra strength and the optimum stitch size for the type and weight of leather being used. Once your jacket is complete, the maker will proudly write their name on the inside label and swing ticket of the jacket so it can be identified as one of their works.
Quality Check
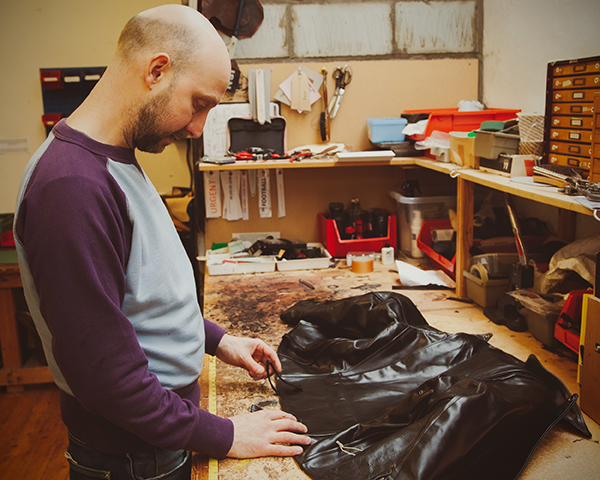
After your jacket is finished, it heads over for its final quality check. The most experienced member of our team (who has been with Aero since the late 1980s) alongside our production manager carry out a rigorous 28-point inspection on your jacket, including alignments, stitch quality and matching to ensure the jacket’s craftsmanship has met the quality standards that are expected of an Aero Label. If your jacket doesn’t meet one of these high standards, we will remake your jacket.
Your jacket is ready for dispatch!
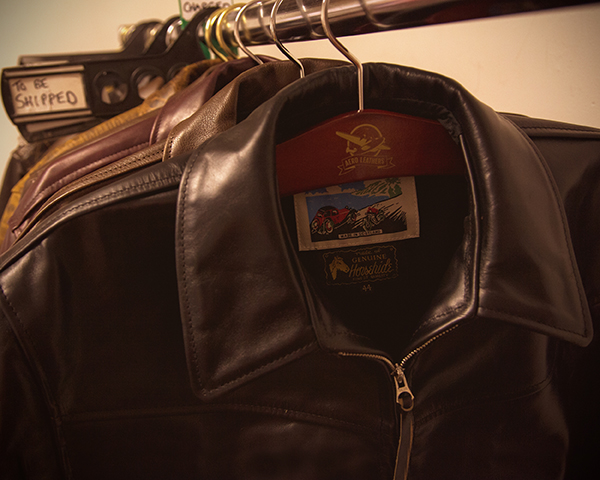
We will contact you as soon as your jacket has left the factory to let you know that your jacket is ready for dispatch and request any remaining balance. Once this has been paid, a member of our dispatch team will carefully pack your jacket and it will be en-route to you via courier within a day! Our selected courier will contact you to let you know a delivery time.
A jacket for life...
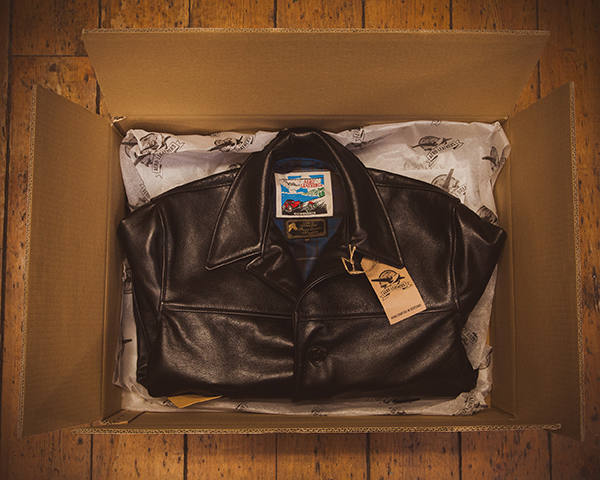
Then, all you need to do is sit tight and wait for your package to arrive! The wait is nearly over — soon, you’ll be opening a box to get the first glimpse of your very own Aero jacket. You’ll get to enjoy that unmatchable experience of trying it on and seeing yourself in your dream jacket for the very first time in the mirror. And as amazing as it looks new, this is just the beginning of a life-long journey with your Aero where it looks better with every wear as the leather breaks in and starts to patina.
Our Guarantee:
We don’t want anyone to own an Aero that they don’t love. If we’ve made a mistake with your jacket outwith our stated measurement tolerances, we will remake it for you at no additional cost. If we’ve made the jacket to your specifications but you’re still not happy with jacket, unless we have advised you during production that heavy customisations have made the jacket non-returnable, we will still remake your jacket, but it may be subject to a 20% restocking charge if we incur additional costs.